安井行生のロードバイク徹底評論 第6回 YONEX CARBONEX vol.10
目次
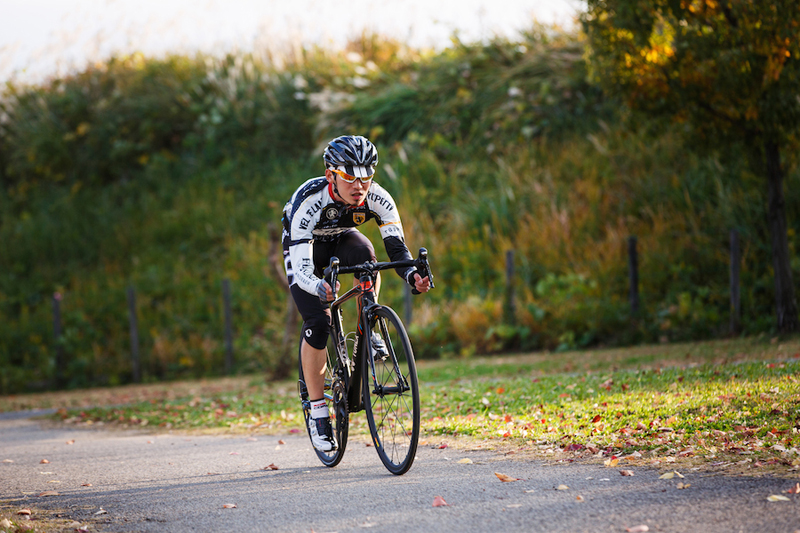
大手スポーツ用品メーカー、ヨネックスがロードフレームを作り始めた。このロードバイク界に異業種参入型ブランドがまた一つ誕生したのである。第一弾は650gの超軽量カーボンフレーム、カーボネックス。設計担当者へのインタビューを交えつつ、この純国産フレームの真実に迫る。
国内生産のメリットとは
設計技術の良し悪しと製造技術の良し悪しは全く別のことだ。いくら優れたアタマで無駄のないフレームを設計したとしても、製造現場がヘボで積層も加圧もグズグズだったら意味がない。机上では最高の走りをするはずのフレームが、カタチにしてみれば月並み以下。そういうことだって十分にあり得る。
超音波探傷機を持つカーボンドライジャパンへ取材に行ったとき、工場の技術者がこんなことを言っていた。「フレームの右と左でチューブの厚みが数mm違うものもあります。何十万も出して買ったオーナーにはとてもじゃないけど見せられません」。設計で左右差を設けたわけではないだろう。厚みの差が数mmもある状態では、設計通りの性能は出ていないだろう。これが現在のカーボンフレームの現実の一端なのである。
おそらくカーボネックスは、設計図通りに正確に作られ、設計者が意図した通りの性能が出ているのだろう。製造時だけでなく、開発時にも国内生産のメリットがあったという。
「テストライダーから意見をもらって2、3週間で修正できることも、国内生産の開発力・製造力ならではといえます。この部分にちょっと積層を足そう、というような細かな設計変更を素早く正確に製品に反映することができるんです」
いいモノが育つ土壌があった
海外工場では、こうはいかないことも多いらしい。設計変更に数か月を要する、細かな変更が思い通りにいかない、そもそも設計通りのモノができない、などの話を聞いたことがある。言葉の壁も大きいだろう。国民性の違いによる認識の差も小さくないだろう。しかし期限は迫ってくる。そのような状態では、成熟不足のまま発売というようなことも起こり得るかもしれない(前述したとおり、最近ではオープンモデルを買ってきてブランドロゴを乗せただけや、フレームメーカーはコンセプトや価格やスペックを決めるだけで主に開発を行うのは工場側という工場依存の開発体制をとるなど、熟成がどうのという以前のケースも増えてきているようだが)。
国内の自社工場であれば、このヨネックスのようにテストの現場、設計の現場、モノづくりの現場が地理的にも意識的にも近く、正確なキャッチボールが幾度となく可能になる。フレームはどんどん煮詰められていく。そうしてどんどんいいモノに育っていく。結果、しっかりと磨き上げられたものを送り出すことができる(もちろん、アジア生産でもしっかりとクオリティコントロールを行い、素晴らしいフレームを作っているメーカーは数多く存在する。名車の誉れ高いスーパーシックスエボやSLR01や新型ターマックだって中国・台湾生産である)。
人件費の安い海外に生産拠点を移せば、もちろんコストを下げることができ、ユーザーにモノをより安く提供できるという大きなメリットが生まれる。しかし、トレックやタイムやコルナゴが今でもトップモデルの自国自社工場生産にこだわっているのには、それなりの理由があるのだろう。「どこで作るか」ではなく「どう作るか」が重要なのだが、やはり本国生産のメリットは存在するのだ。
国内の自社工場であれば、このヨネックスのようにテストの現場、設計の現場、モノづくりの現場が地理的にも意識的にも近く、正確なキャッチボールが幾度となく可能になる。フレームはどんどん煮詰められていく。そうしてどんどんいいモノに育っていく。結果、しっかりと磨き上げられたものを送り出すことができる(もちろん、アジア生産でもしっかりとクオリティコントロールを行い、素晴らしいフレームを作っているメーカーは数多く存在する。名車の誉れ高いスーパーシックスエボやSLR01や新型ターマックだって中国・台湾生産である)。
人件費の安い海外に生産拠点を移せば、もちろんコストを下げることができ、ユーザーにモノをより安く提供できるという大きなメリットが生まれる。しかし、トレックやタイムやコルナゴが今でもトップモデルの自国自社工場生産にこだわっているのには、それなりの理由があるのだろう。「どこで作るか」ではなく「どう作るか」が重要なのだが、やはり本国生産のメリットは存在するのだ。